While we might be familiar with the big names heralded for spearheading the cell-based food sector, it's the lesser-known companies with revolutionary innovations that are also catalysing major disruption.

In The Cell Base's very first instalment of ‘Start-up spotlight' we speak to Will Milligan, founder of Extracellular, a Bristol, UK-based start-up supporting cell-based meat and seafood companies with development and scale-up capabilities.
Can you introduce Extracellular and highlight its mission and core objectives, please?
Extracellular is a contract development and manufacturing organisation dedicated to supporting cultivated meat and seafood companies with our development and scale-up capabilities. What that practically means is, we provide R&D as a service, focused on cell and media development, with a core focus on process optimisation and scale-up. Our mission is to support cultivated meat and seafood companies in getting to market years faster and millions of dollars cheaper through our services.
What led to the establishment of Extracellular and why did you choose to focus on cultivated meat?
My background is in process development and scale-up for biopharma, and that skillset is exactly the skillset needed to enable cultivated meat and seafood products to come to market. We're basically using stem cell technology for food rather than therapeutics. And with that skillset in mind, I really wanted to support a large number of companies. Really, Extracellular was established to support as many companies as possible.
We focused on cultivated meat as it has a large potential impact to reduce carbon emissions for food production. And as a guilt-ridden millennial, I stress about my impact on the planet and wanted to work on something that would hopefully leave the planet in a better place than how we found it. Additionally, in the cultivating space, there's a huge underserved market for development services and scale-up capabilities. It's very technically challenging, so it takes that deep expertise to really support these companies effectively. Given that so many companies were vertically integrated, and the new wave of companies coming through needed the services, we established Extracellular.
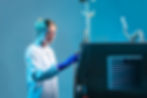
What are the unique benefits of Extracellular's services and what kind of impact do you believe the company has had or could potentially have in the future?
We're focused on having fit-for-purpose capabilities to support the industry, which means we have high-end bio-tech capabilities, but at a low cost. We already have 15 customers around the world, across eight countries and four continents, so we already have this broad client base, and we are helping them accelerate their R&D pipeline. We're having an impact on the development of cultivated meat today around the world.
We aim to help these companies get to large-scale, and we can help them get there much quickly and cost-effectively. Ultimately, we hope that no company in the industry needs to build a pilot facility in the next five years because we can build those capabilities. They can save that money on capital expenditure and team build-out and the cost of the facility and the time it takes. We think we can help really enable the large-scale production of cultivated meat and seafood.
What are the essential technologies and capabilities that make up Extracellular's services?
We have high throughput capabilities for cell and media development. We use liquid handlers and high-content imaging systems as well as other automation solutions to screen large numbers of conditions very quickly. We can screen up to 1,000 different cell types or media formulations in a given study. For bioreactor optimisation, we have a number of parallel bioreactors, so we can test between 12 and 24 bioreactors in parallel, to do the equivalent of six months' worth of work in two weeks. That really allows us to do high-throughput, fast studies for customers. On the scale-up side of things, we have the ability to run one-, ten-, 100- and 200-litre bioreactors. At the end of this year, we'll have 2000-litre bioreactors installed for the large-scale production of cultivated meat.
Sustainability and ethical considerations play a significant role in the cell-based food sector. How does Extracellular approach these aspects in its operations?

We have big focus on sustainability in the lab, we have a dedicated team member to support lab operations and sustainability, with a big focus on reducing our impact on the planet. For instance, we recycle far more plastic than would typically be expected in research labs, and we also repurpose a lot of food and pharma equipment and consumables, to save them from going to landfill. That's a big focus of ours in the lab.
On the ethical front, we're really trying to support our customers in removing animal components from their media formulations and finding alternatives that can promote cell growth. So, we really collaborate with our customers to try and come up with more ethical, more sustainable solutions. Simultaneously, we try to design the best processes possible. Because, ultimately, the potential sustainable impact of cultivated meat will only come when we can produce large quantities of cells at scale. And really, that's where we think we can have the biggest impact.
Has Extracellular encountered any challenges on its journey so far? How did you work to navigate or overcome these obstacles?
It's a super challenging fundraising environment at the moment. For us, we got through it by focusing on customer value rather than investor expectations. That meant that we really set out to offer the best services at the lowest price points to support other companies in cultivated meat in achieving their R&D and fundraising goals. We take the opinion that, you know, if our customers succeed, then we can succeed.
Hiring the right team is essential in developing these products and processes. I think we have a great culture here that really empowers researchers to think creatively and collaboratively. The projects that are the most successful are the ones where we bring our expertise in development and scale-up, and our customers bring their scientific expertise, and together, we create something that we couldn't achieve individually.
Collaboration with the scientific community can be crucial in advancing cell-based technologies. Can you shed light on Extracellular's engagement with researchers and scientists?
We want to support better research and more solutions for cultivated meat and seafood. Part of that is making sure that researchers have the right skills to develop better products, whether that's media formulations, cell lines, or bioreactors, for example. That's why we collaborated with Multus to produce low-cost, license-free cell banks that are relevant to the industry. In doing so, there are now a number of research organisations across the UK and globally, that use these cells to try and develop better products. We do research and share what we find and troubleshoot them through it – we really think that collaborating is the best way to advance the industry.
What exciting developments or plans does Extracellular have in the pipeline and what can we expect to see in the coming months?
In the next couple of months, we expect to have our 2000-litre bioreactors operational and producing cultivated meat. Beyond that, we are planning our international expansion to build food-grade facilities in North America and Asia. We expect to have multiple sites around the world in the next three to five years commercially producing cultivated meat products.